How Plywood is Manufactured? (Process, Types and Advantages)
Plywood – the unsung hero of construction and design! Ever wondered how this versatile material comes to life? Well, buckle up for a fascinating ride through the world of plywood manufacturing.
We’re about to spill the beans on the entire process – from handpicking the finest logs to whipping up those rock-solid composite panels.
It’s like a behind-the-scenes tour of how plywood becomes the backbone of modern construction and design.
So, hop on board as we uncover the craftsmanship, precision, and science that turn humble wood veneers into a superstar in the world of building and design!
Key Takeaways
- Plywood is a versatile building material made from thin wood veneers glued together with cross-lamination for strength and stability.
- It’s typically crafted from softwoods like pine, fir, or spruce, with veneers arranged to prevent warping.
- Used widely in construction, furniture, and more due to its strength, durability, and affordability.
- Plywood can support heavy loads, making it suitable for various applications.
- It’s resistant to warping, making it ideal for furniture and cabinetry where stability is crucial.
- Plywood’s versatility extends to marine applications, outdoor projects, and signage.
- Manufacturing involves selecting high-quality logs, slicing veneers, drying, gluing, and pressing.
- Adhesives like phenol-formaldehyde ensure water resistance, crucial for marine applications.
- Various plywood types exist, including hardwood, softwood, marine, sanded, and structural plywood.
- Proper sealing prevents mold and rot, while quality control ensures the product’s strength and reliability.
What is plywood?
You know plywood, right? It’s that awesome stuff made by stacking super-thin wood layers and gluing them together.
But here’s the secret sauce: they twist those layers just right, up to 90 degrees apart, in a fancy process called cross-lamination. That’s what makes plywood tough as nails!
So, what’s it made of? Usually, it’s all about the softies – pine, fir, or spruce. They take these logs, strip off their bark, and slice ’em into those ultra-thin sheets using a rotary peeler.
Afterward, they dry those sheets to the perfect moisture level and layer them up. But here’s the trick – each layer’s grain goes in a different direction from the one above it.
This little move? It’s the superhero move that stops plywood from going all wonky and wobbly on you. Cool, right?
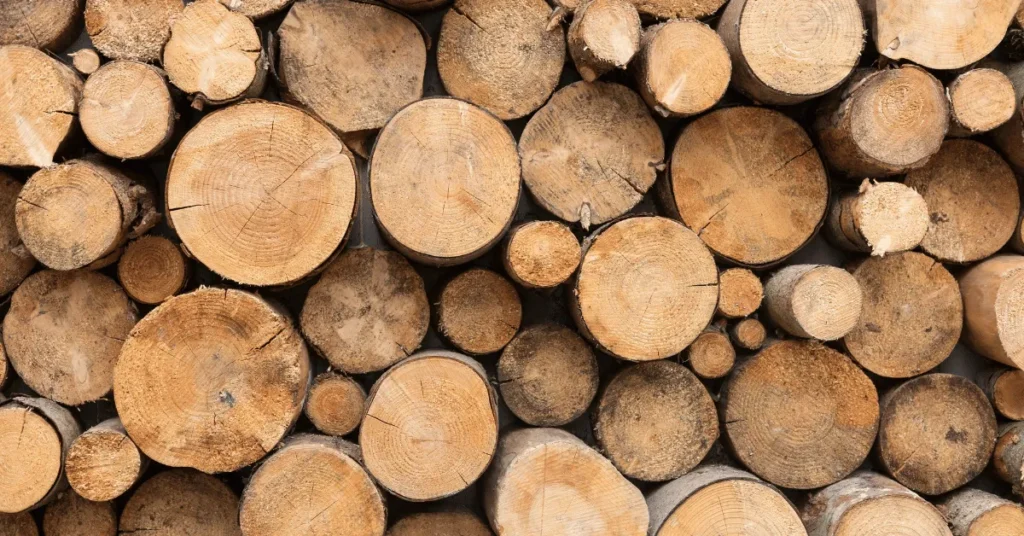
Next up in the plywood-making magic: those thin veneers get cozy with some water-resistant glue. They’re all glued up and ready to rock!
But hold onto your hard hat – here comes the hot press! They pop the plywood in there for a few hours to set that glue just right.
Once it’s all set, they give it a little trim and a nice sanding to make it all smooth and pretty. Easy-peasy, right?
Plywood exhibits remarkable versatility, finding utility across a spectrum of applications, such as:
- Construction
- Furniture making
- Boat building
- Cabinetry
- Signs
- Shelving
- Roofing
More about plywood
So, let’s talk plywood – it’s like the superhero of building materials. It’s tough, light as a feather, and a total breeze to work with. And the best part? It won’t break the bank, making it the top pick for all sorts of projects.
Plywood is basically the Hulk of materials – super strong and built to last. It can handle a ton of weight and stress without even breaking a sweat.
Plus, it’s like the Zen master of stability. No warping or twisting here! So, if you’re into furniture or cabinets that stay in tip-top shape, plywood’s your go-to.
And the best part? It’s a jack-of-all-trades. Whether you’re tackling an indoor project or taking on the great outdoors, plywood’s got your back. And it won’t break the bank either, perfect for those budget-friendly projects!
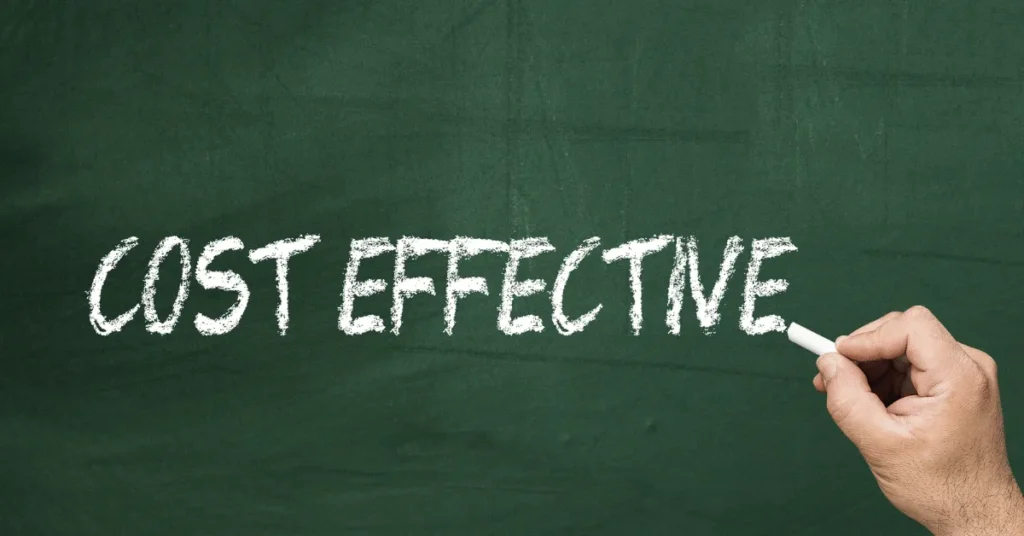
Here are some of the drawbacks of using plywood:
Now, let’s get real about plywood. It’s like the little brother of solid wood – not as tough, but it gets the job done. You see, it’s made of these thin wood layers all glued up together.
But, fair warning, it’s not always a walk in the park to work with. Those multiple layers can be a bit tricky, and cutting and sanding? Well, let’s just say it’s not a piece of cake.
Oh, and here’s the scoop: if plywood isn’t sealed up properly, it can get kinda sensitive to water. That means it might throw a fit and warp or rot if it gets wet.
But hey, it’s not all bad news. Plywood’s still a champ for loads of projects, and it won’t break the bank. Just remember to weigh the pros and cons before diving in.
Do You Know?
Plywood’s strength and versatility stem from its cross-laminated construction, where wood veneers are layered with their grains rotated for enhanced resilience, stability, and resistance to warping.
Notably, marine plywood’s specialized treatment grants it exceptional durability against moisture and decay, making it the ideal choice for water-exposed applications like boats and docks.
Beyond its reliability, plywood’s weight corresponds to its robustness, making it heavier than materials like MDF or particleboard, but ultimately stronger.
Whether used in furniture, marine structures, outdoor projects, or even compared to other sheet materials, plywood’s unique qualities position it as a dynamic and enduring building material.
Where is plywood used?
Alright, let’s break it down – plywood is like the Swiss Army knife of materials. It’s everywhere, indoors and outdoors, and it’s got some serious game.
In the construction world, it’s the go-to for subflooring, sheathing, and roof decking. Tough as nails and won’t empty your wallet – builders love it.
But hold onto your hat, it’s also a rockstar in furniture making. Strong, lightweight, and a breeze to work with, it’s the secret sauce behind tables, chairs, cabinets, and bookcases.
And it’s not afraid of a little water – that’s why it’s a hit in marine applications. Boats, docks, you name it. Plywood’s the unsung hero keeping things afloat.
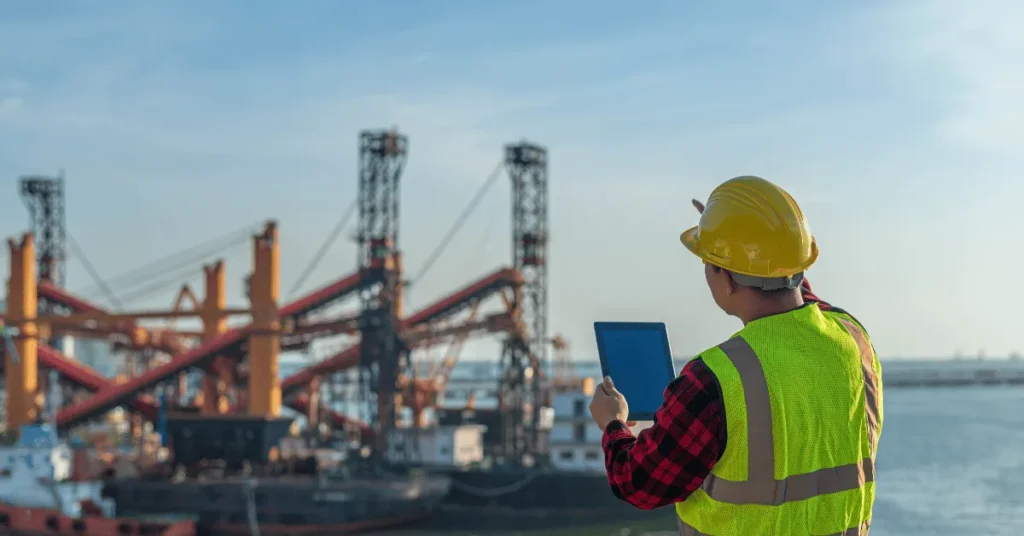
Hey, plywood isn’t just an indoor thing – it’s got an outdoor side too. It’s like the all-weather buddy you can count on. Decks, fences, and all sorts of outdoor structures, they owe a nod to plywood for taking on the elements.
And when it comes to signs and displays, plywood’s got some serious street cred. Strong, light, and easy to jazz up with paint – it’s the canvas for custom signs and eye-catching displays.
So, plywood’s the real deal, whether you’re building indoors or braving the great outdoors. It’s strong, tough, and won’t break the bank – a top pick for tons of projects.
How plywood is manufactured? Step-by-step guide
Plywood is like the Swiss Army knife of building materials – it’s versatile, tough, and won’t break the bank.
Picture this: it’s made by layering thin wood veneers and sticking them together with super-strong glue. The result? A composite panel that’s like a blank canvas for all sorts of projects.
Curious about how it’s made and what you can do with it? Stick around, and we’ll break it down for you.
Sourcing the Raw Materials:
So, making plywood is a bit like picking the best players for your dream sports team. You start by choosing top-notch logs from different tree types like pine, oak, or maple. Why? Well, it’s all about getting that perfect plywood with the right strength and quality.
Debarking and Peeling the Veneers:
Next up, after picking the prime logs, it’s time for a little makeover. They get rid of that rough bark in a process called debarking.
Then, the logs meet a sharp blade that works some magic. It peels off super thin layers of wood, like those fancy potato peelers but way thinner—about 1.0 to 1.5 millimeters thin.
These thin wood sheets are what we call veneers, and they’re ready for the next steps.
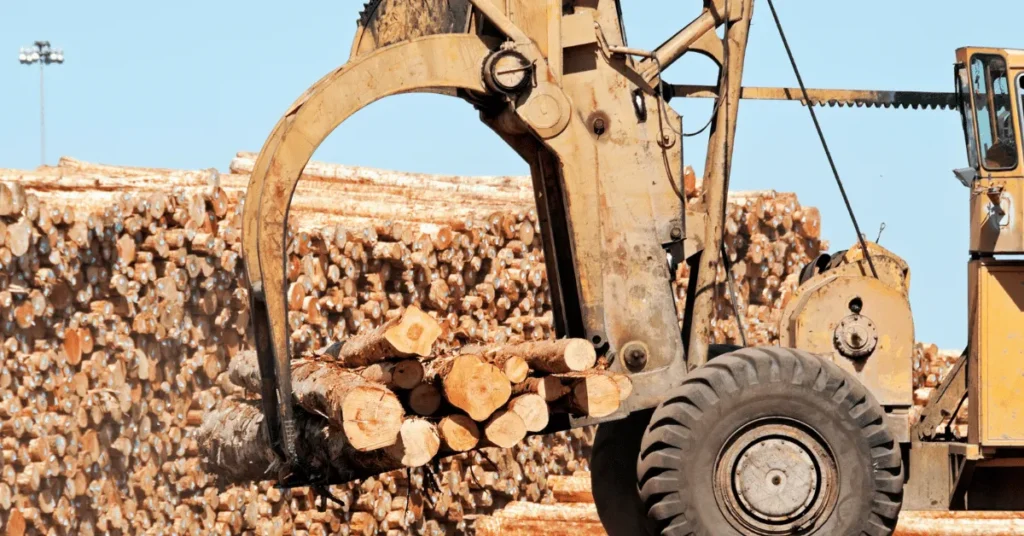
Sorting and Grading:
Now, here’s where the veneers get their report cards. They go through a careful sorting and grading process based on stuff like how awesome they look, their thickness, and overall quality. We’re talking about some serious scrutiny here.
Only the crème de la crème veneers make the cut for the final plywood sheets. Any veneer that’s got knots, oddities, or issues might get a rain check for some other gig or simply hit the road.
Preparation of Adhesive:
Now, when it comes to gluing those veneers together, we’re talking about some serious bonding business. They use strong adhesives like phenol-formaldehyde or urea-formaldehyde resins – you know, the gluey stuff.
But it’s not just plain glue; they mix in some additives to make sure it’s extra sticky and tough. And here’s the deal: the type of adhesive they choose can make or break how well the plywood handles moisture, heat, and all that Mother Nature throws at it.
Layering and Pressing:
So, after they’ve sorted those veneers and picked the winners, it’s time to stack ’em up like a sandwich. They slather adhesive between each layer, and here’s the trick: they make sure the grain in one layer goes one way and in the next, it goes all different.
That’s the secret sauce for giving plywood its muscle and stability. Then, they toss the whole stack into a hydraulic press, crank up the heat and pressure, and boom – you’ve got yourself a solid plywood panel.
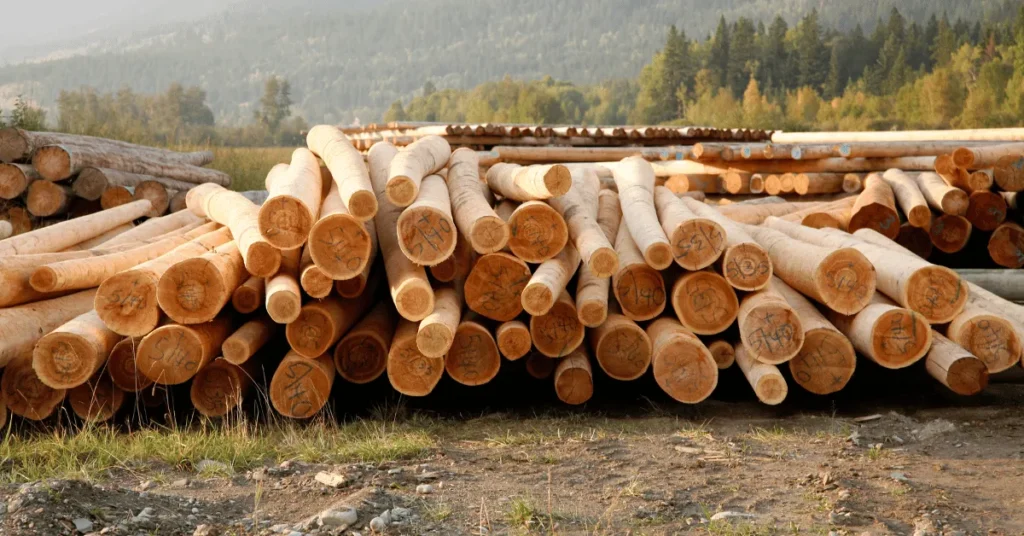
Curing and Trimming:
Once that plywood stack comes out of the press, it’s like a spa day for wood. They let it chill under heat and pressure for a few hours, and voila! You’ve got yourself a plywood panel that’s as strong as it gets.
Once the curing process is complete, the plywood is trimmed to the desired size to remove excess edges or irregularities.
Sanding and Quality Control:
Following trimming, the surface of the plywood panel is sanded to achieve a smooth and uniform texture. Sanding also contributes to the overall appearance and finish of the plywood.
The final product then undergoes rigorous quality control and inspection to check for defects, delamination, and adherence to industry standards.
Types of Adhesives Used:
- Phenol-Formaldehyde: This adhesive is highly water-resistant and suitable for applications where the plywood might be exposed to moisture, such as in marine applications.
- Urea-Formaldehyde: This adhesive is commonly used for indoor applications and offers good bonding properties. However, it is less water-resistant than phenol-formaldehyde.
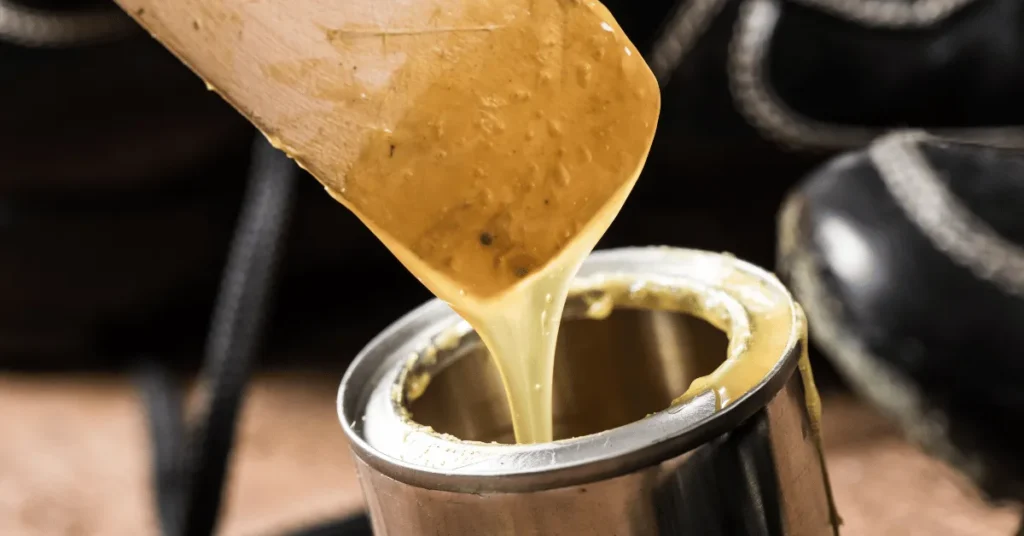
Quality Control Measures:
So, here’s the deal with making top-notch plywood:
Sorting the Good Stuff: They pick out the cream of the crop when it comes to veneers. Only the best-looking and strongest ones make the cut.
Glue It Right: You can’t have weak spots, so they make sure that glue is spread evenly between the layers. No lumps or gaps allowed.
Bake ‘Em to Perfection: It’s like baking a cake, but with wood. They use the right amount of heat and pressure to create that rock-solid bond.
Let It Cure: Like a fine wine, plywood needs some time to reach its full potential. They give it time to cure properly, so it’s tough as nails.
The Final Check: Before it hits the market, every sheet of plywood goes through a thorough check. They’re looking for any defects or issues to make sure you get the good stuff.
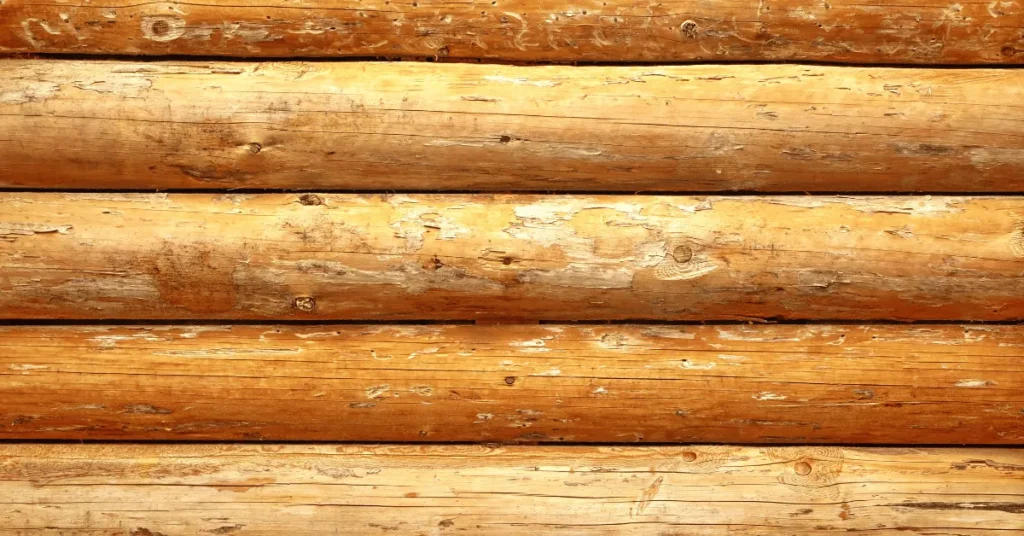
So, here’s the secret sauce: Plywood makers keep a close eye on quality at every step. That way, you end up with plywood that’s tough, long-lasting, and ready for whatever you throw at it.
What are the different types of plywood?
Let’s talk plywood flavors! There’s a bunch of them, each with its own specialty:
Hardwood Plywood: This one’s the tough guy. Made from hardwood veneers like maple, oak, or birch, it’s your go-to for heavy-duty stuff. Think furniture, flooring, and cabinets.
Softwood Plywood: A bit more easygoing and budget-friendly, softwood plywood rocks softwood veneers like pine, spruce, or fir. It’s perfect for temporary structures, sheathing, and subflooring.
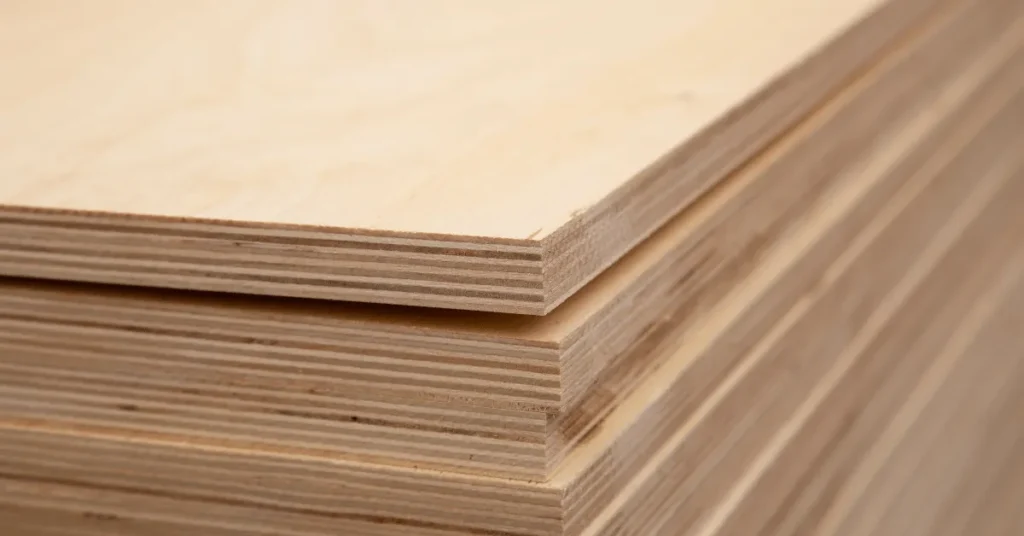
Marine Plywood: This one’s ready for a splash. Made with special veneers that laugh in the face of moisture and decay, it’s the go-to for water-loving projects like boats, docks, and all things marine.
Sanded Plywood: Meet the smooth operator. Sanded on both sides, it’s all about that sleek finish. Perfect for projects where looks matter, like classy furniture and stylish cabinets.
Structural Plywood: The strong and sturdy buddy. Built tough with thicker veneers and super-strong glue, it’s got your back when you need to hold up heavy loads. Think roof sheathing and subflooring – it’s got your structure sorted.
The manufacturing process
Let’s demystify the plywood-making process, shall we? It might tweak a bit depending on the plywood flavor, but the core steps stay rock-solid.
First, we pick primo logs of the wood type we fancy. Then, we strip off their bark and slice ’em thin as a wafer with a rotary peeler. Easy peasy!
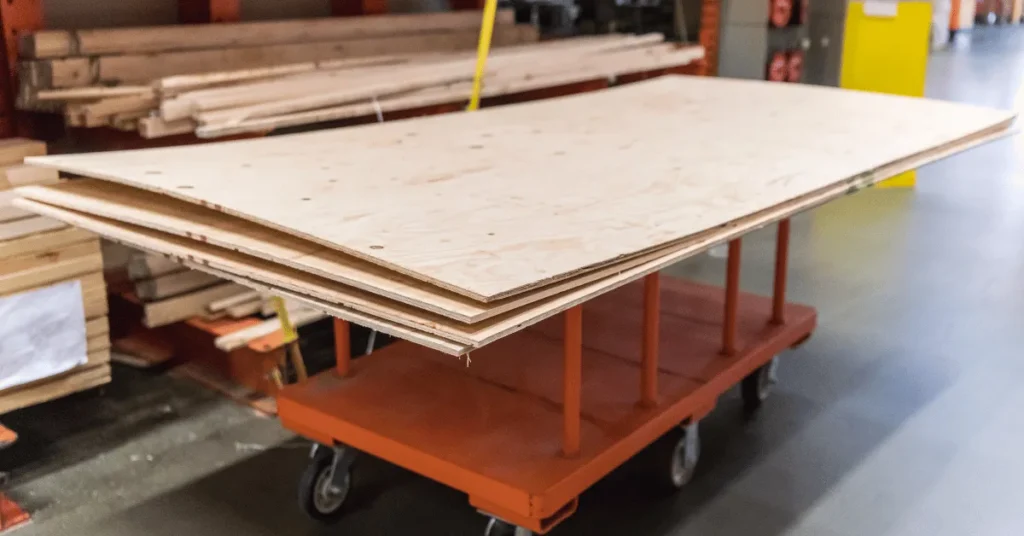
Next up, those thin veneers get a spa day – we dry ’em out just right. Then, we stack ’em up, making sure each layer’s grain is cozy with its neighbor, but they’re all perpendicular-like.
Now, it’s glue time! We slather on some serious adhesive mojo, like phenol-formaldehyde or urea formaldehyde, to make sure those layers stick together like BFFs.
Time for the grand squeeze! We press and bake the whole gang under heat and pressure. Last but not least, we give it a good old sanding for that silky-smooth finish. Voila!
The advantages
Plywood is like the superhero of building materials. It’s super strong, can take on the toughest challenges, and doesn’t break the bank.
Whether you’re building furniture, flooring, or even a roof, plywood’s got your back. It’s tough, versatile, and won’t empty your wallet.
The disadvantages
Now, let’s talk about plywood’s not-so-great side. It’s a bit on the heavy side compared to some other sheet materials like MDF or particleboard. Plus, it’s not a fan of moisture, so you’ve got to make sure it’s well-sealed to keep it in top shape.
But hey, it’s still a champ when it comes to versatility, affordability, strength, and durability. So, a little extra weight and a need for some waterproofing won’t hold plywood back.
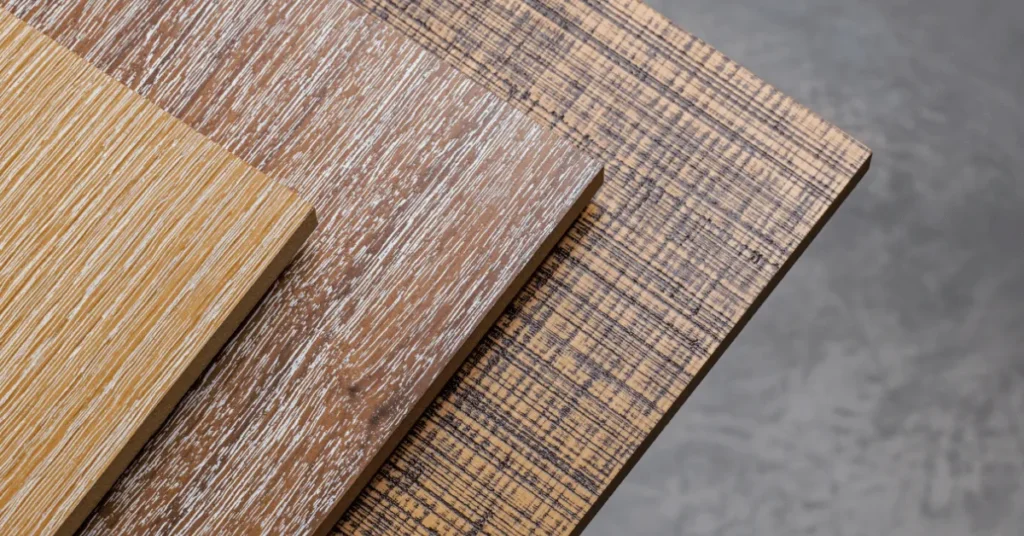
When you’re picking plywood, just think about what type suits your job best. Easy, right?
What are the different sizes of plywood?
There are different sizes of plywood available, each with its specific uses.
- 4′ x 8′: This is the most common size of plywood and is used for a variety of applications, including subflooring, sheathing, and furniture making.
- 5′ x 5′: This size of plywood is often used for cabinetry and other projects where a smaller sheet is needed.
- 6′ x 8′: This size of plywood is used for larger projects, such as roofing and siding.
- 8′ x 8′: This size of plywood is the largest and is used for very large projects, such as commercial buildings.
Plywood comes in all sorts of sizes and thicknesses, from as thin as 1/8″ to a solid inch. Remember, the thicker it is, the stronger it gets.
Check out this handy table for a quick rundown of plywood sizes and what they’re typically used for:
Size | Thickness | Typical Uses |
---|---|---|
4′ x 8′ | 1/8″ to 1″ | Subflooring, sheathing, furniture making |
5′ x 5′ | 1/8″ to 1″ | Cabinetry, other projects where a smaller sheet is needed |
6′ x 8′ | 1/8″ to 1″ | Roofing, siding |
8′ x 8′ | 1/8″ to 1″ | Commercial buildings |
Can plywood mold or rot?
Absolutely, plywood can start to mold or rot if you don’t give it some love and proper sealing. You see, plywood is crafted from wood veneers bonded together with resin. If that resin isn’t protected, moisture can sneak in, and that’s when trouble brews.
So, here’s the deal: to keep your plywood in tip-top shape, make sure to give it a good seal with a water-resistant sealant. That way, you’ll keep mold and rot at bay, and your plywood will stay strong and reliable.
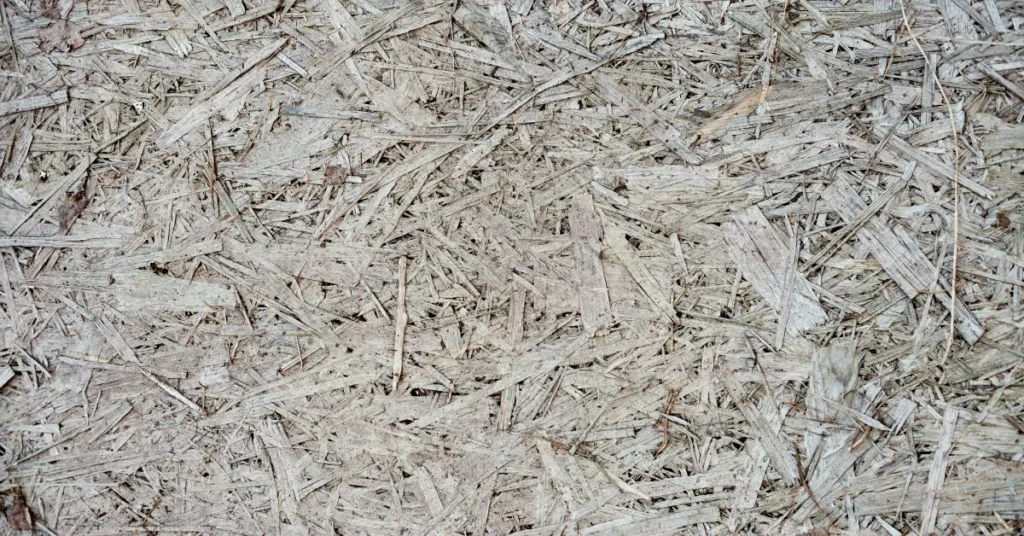
You’ve got a variety of water-resistant sealants to pick from, so here’s the scoop: go for one that’s made especially for plywood. And when you’re slapping that sealant on, don’t forget to show all sides of the plywood some love, including those edges.
Now, if you’ve got plywood that’s already gone moldy or started to rot, don’t procrastinate. Get rid of it and bring in some fresh plywood. Mold and rot can be real party crashers, and you don’t want them spreading to other materials. Stay ahead of the game!
Here are some tips for preventing plywood from molding or rotting:
- Use a water-resistant sealant on all sides of the plywood, including the edges.
- Store plywood in a dry place.
- Avoid getting plywood wet.
- If plywood gets wet, dry it out as soon as possible.
- Inspect plywood regularly for signs of mold or rot.
- Replace plywood that is moldy or rotting.
With these pointers in your toolbox, you’ll be the plywood pro, keeping that stuff mold and rot-free while giving it some extra mileage.
How does plywood compare with other products?
Alright, to tackle this issue, I rolled up my sleeves and dug into some research. Voila! Here’s the lowdown on plywood and how it stacks up against other sheet materials.
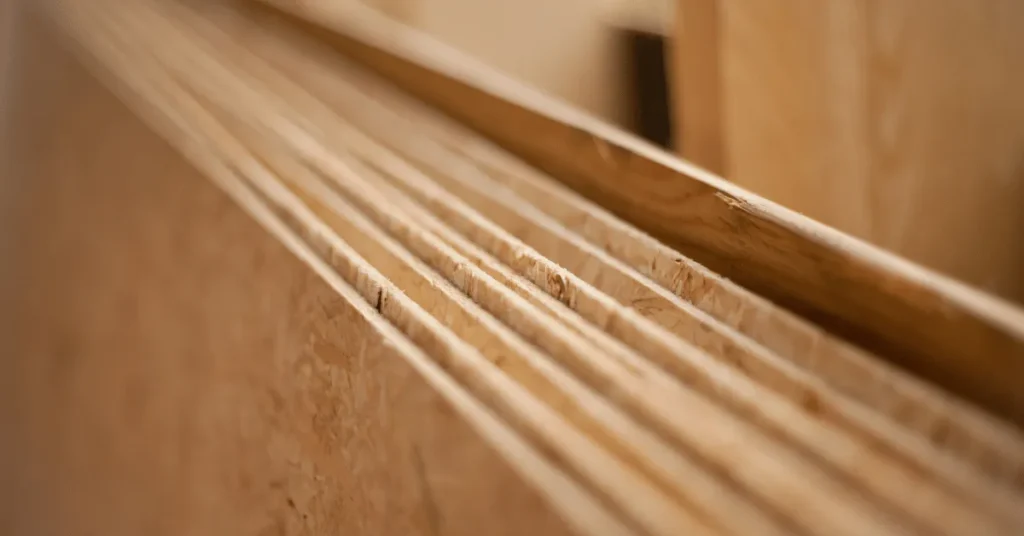
Let’s chat about plywood, the Swiss Army knife of sheet materials. It gets compared to its buddies – MDF, particleboard, and OSB. Plywood? Well, it’s basically layers of wood veneer glued together, giving it muscle and a knack for resisting moisture better than the others.
Then there’s MDF, smooth operator, made by squishing wood fibers with resin. Not the Hulk, though, so it’s not as tough as plywood and doesn’t handle water well.
Particleboard? It’s like the budget option, created by smooshing wood particles with resin. Wallet-friendly, sure, but not the powerhouse plywood is, and it doesn’t laugh off moisture.
Now, OSB – oriented strand board – is like the jock of the group, with wood strands bonded together by resin. Tough? Absolutely. But it’s not the driest guy in the room.
Comparison with other products
Want the deets? Check out the handy table below for the full scoop:
Feature | Plywood | MDF | Particleboard | OSB |
---|---|---|---|---|
Strength | Strongest | Weaker | Weakest | Stronger than particleboard, but weaker than plywood |
Durability | Most durable | Less durable | Least durable | More durable than particleboard, but less durable than plywood |
Moisture resistance | Most moisture resistant | Not moisture resistant | Not moisture resistant | More moisture resistant than MDF and particleboard, but less moisture resistant than plywood |
Price | Most expensive | Most affordable | Least expensive | Least expensive |
Appearance | Natural | Smooth, uniform | Rough, unfinished | Rough, unfinished |
So, what’s the verdict? Well, it all boils down to your project’s needs and the dollars in your pocket. Need something tough, durable, and not afraid of a little water? Plywood’s your pal.
On a budget? MDF or particleboard could be your wallet’s best friend. And if you’re all about that smooth, uniform look, MDF’s got your back. It’s like a choose-your-own-adventure in the world of materials!
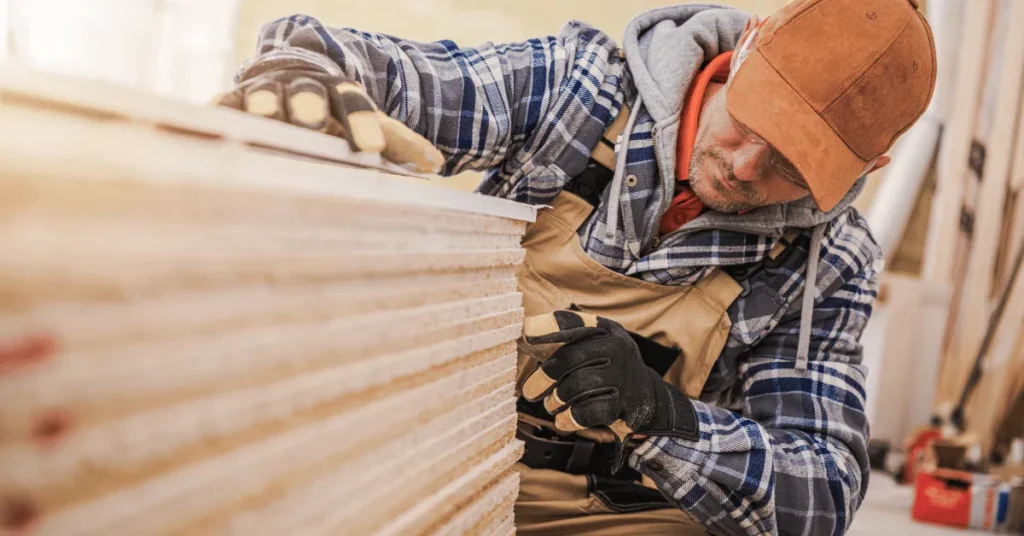
Important FAQs
Cross-lamination involves arranging wood veneers with their grain direction rotated up to 90° to each other. This process provides plywood with enhanced strength, stability, and resistance to warping.
Marine plywood is specially treated to resist moisture and decay, making it an excellent choice for water-exposed applications like boats, docks, and marine structures. Its durability in wet conditions sets it apart from standard plywood.
Plywood is generally heavier than MDF or particleboard due to its layered structure. However, its added weight often corresponds to increased strength and durability.
Plywood’s resilience against the elements, owing to its layered composition and water-resistant adhesive, makes it an ideal choice for outdoor projects where exposure to weather is a concern.
Plywood’s fire resistance varies depending on its composition. While plywood can be treated to enhance its fire-resistant properties, materials like gypsum board or drywall are typically better options for fireproofing.
Final Thoughts
Plywood, folks, it’s more than just sheets of wood glued together. We’re talking about a versatile, tough cookie of a building material.
Imagine this: logs picked with precision, a peeling process that’s almost an art form, and the secret sauce—strong adhesives. And don’t forget the meticulous quality checks. Only the A-list plywood gets the green light.
Now, why should you care? Plywood isn’t just strong; it’s your stability buddy, your versatile sidekick, and your wallet’s best friend. From building skyscrapers to crafting cozy furniture, plywood does it all.
But hold on, it’s not invincible. Get it wet, and you’ve got trouble. So, keep it dry or seal it up.
And when it comes to the competition—MDF, particleboard, OSB—plywood doesn’t break a sweat. It’s like the superhero of the wood world.
In a nutshell, plywood is the result of human smarts meeting Mother Nature’s goods. It’s the unsung hero behind modern buildings and cool designs, ready for action in your next project.
Images by: Canva.com